Lean Thinking
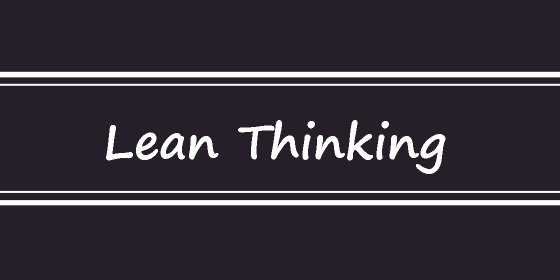
Lean Thinking is a management philosophy and approach that originated from the Toyota Production System (TPS) and was popularized by the book “The Machine That Changed the World” by James P. Womack, Daniel T. Jones, and Daniel Roos. Lean Thinking focuses on creating value for customers while minimizing waste and optimizing processes to achieve better results.
Key principles of Lean Thinking include:
- Value: Focus on understanding what customers perceive as value and align all activities and processes to deliver that value. Eliminate activities that do not add value to the end product or service.
- Value Stream: Identify and map the end-to-end value stream, which represents the sequence of processes and activities required to deliver a product or service to customers. Analyze the value stream to identify opportunities for improvement and waste reduction.
- Flow: Optimize the flow of work through the value stream by reducing interruptions, delays, and bottlenecks. Ensure that work moves smoothly and efficiently from one process step to the next.
- Pull: Operate based on customer demand rather than pushing products or services into the system. Use pull systems to produce only what the customer wants, when they want it.
- Perfection: Strive for continuous improvement and perfection in all processes and activities. Encourage a culture of constant learning and innovation.
- Respect for People: Value and empower employees as a valuable resource for process improvement and problem-solving. Respect their knowledge, creativity, and expertise.
- Continuous Improvement (Kaizen): Pursue small, incremental improvements in processes and operations regularly. Encourage all employees to participate in problem-solving and contribute to making improvements.
Lean Thinking is widely applied in various industries beyond manufacturing, including healthcare, software development, construction, and service-oriented businesses. It encourages organizations to be more customer-focused, adaptive, and responsive to changing market conditions. By identifying and eliminating waste and inefficiencies in processes, Lean Thinking helps organizations deliver products and services more efficiently, with higher quality, and at lower costs. The focus on continuous improvement and respect for people fosters a culture of learning, collaboration, and employee engagement, leading to sustainable long-term success.