Lead Time
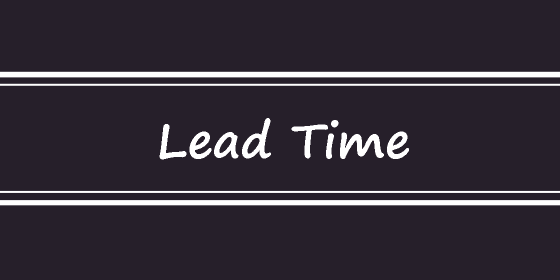
Lead Time is a critical metric used to measure the elapsed time between the initiation of a work item and its completion. It is a fundamental concept in Lean and Agile methodologies and is commonly used in Kanban systems to evaluate workflow efficiency and identify areas for improvement.
Lead Time includes the entire duration a work item spends in the system, from the moment it is requested or added to the backlog until it is delivered and ready for use or deployment. It provides a holistic view of the time taken to fulfill a customer request or complete a task.
Key points about Lead Time include:
- Customer Perspective: Lead Time is often measured from a customer’s perspective, reflecting the time it takes for a customer’s request to be fulfilled. For software development, it can represent the time from a user story’s inception to its implementation and delivery.
- Process Efficiency: Lead Time is a crucial indicator of process efficiency. Shortening the Lead Time often implies that the workflow is more responsive, less subject to delays, and delivers value more rapidly.
- Data-Driven Decisions: Lead Time data helps teams make data-driven decisions and identify bottlenecks or inefficiencies in the workflow. It can highlight areas where process improvements or optimizations are needed.
- Variance: Lead Time can vary depending on the type and complexity of work items. Understanding this variance helps teams set realistic expectations and plan accordingly.
- Cycle Time vs. Lead Time: While similar, Lead Time and Cycle Time are not the same. Cycle Time refers to the time taken to complete a work item after it has entered an active, work-in-progress state. Lead Time includes Cycle Time but also considers the time a work item spends in queues or waiting to enter the active state.
- Impact on Predictability: Monitoring Lead Time over time helps teams establish a predictable flow of work, making it easier to forecast future delivery dates and plan workloads effectively.
To improve Lead Time, teams may adopt practices such as:
- Work-in-Progress (WIP) Limits: Setting WIP limits on different stages of the workflow to prevent overloading and reduce wait times.
- Continuous Improvement: Regularly inspecting and adapting the process to identify opportunities for streamlining and optimizing the workflow.
- Value Stream Mapping: Analyzing the entire value stream to identify areas for improvement and reduce non-value-added activities.
Shorter Lead Time generally indicates a more efficient and responsive workflow, leading to faster delivery of value to customers. Continuous monitoring and improvement of Lead Time help organizations become more adaptive and customer-centric, leading to improved customer satisfaction and increased competitiveness.